1秒短縮で1億円超のコスト削減もー
射出成形の現場ではサイクルタイム1秒の短縮が、コストに大きく関係してきます。
たとえば毎月500万個の量産品では1秒サイクルタイムを短縮することで年間約1億1,667万円のコスト削減につながるという試算もあります。
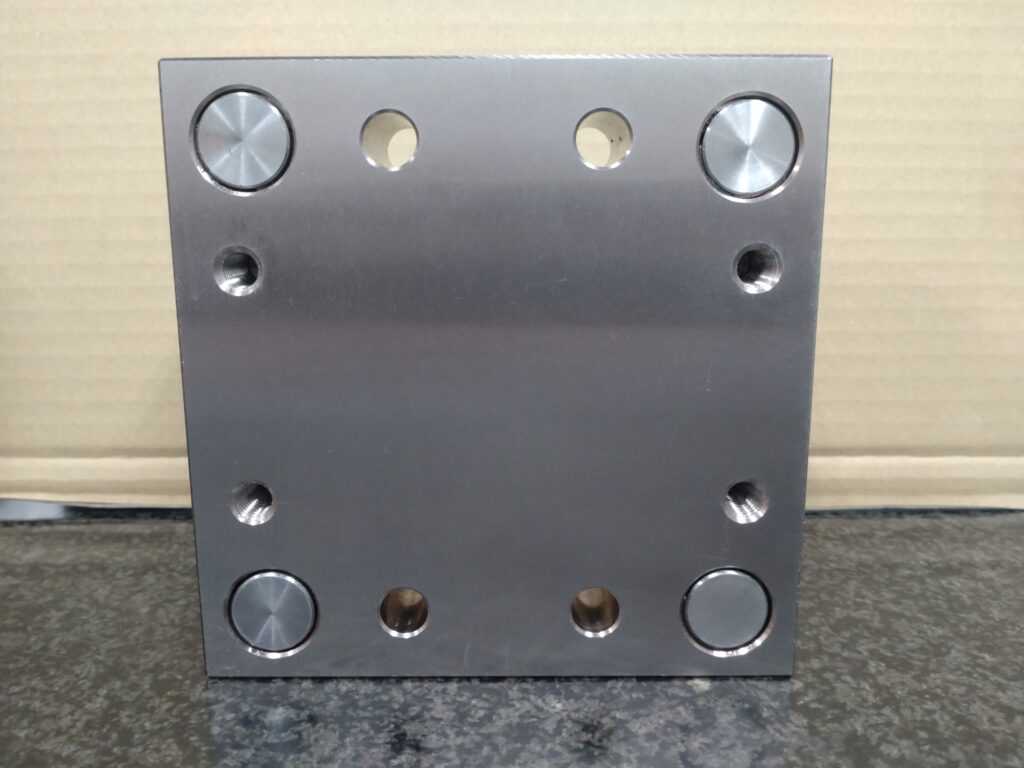
サイクルタイムとはー
金型におけるサイクルタイムとは、射出成形における1ショット(金型を閉じてから次のショットを開始するまで)にかかる一連の工程時間を指します。生産効率やコスト、品質管理に重要な指標であり、成形工場ではサイクルタイムの最適化が重要視されます。
サイクルタイムを短縮するにはー
ガラスファイバー強化樹脂(GF樹脂)の成形では、サイクルタイムの短縮と金型の耐久性が大きな課題です。
従来、プリハードン鋼「NAK80」などが多く使用されてきましたが、冷却性や摩耗耐性には限界がありました。
サイクルタイムの短縮方法:
- 冷却回路の最適化:冷却水の流れを効率的にすることで、冷却時間を短縮できます。
- 金型構造の工夫:ラック式金型など、型開きと同時に離型できる構造にすることで、サイクルタイムを短縮できます。
- 成形機の性能向上:成形機の速度や精度を向上させることで、充填時間や型締め時間を短縮できます。
- 成形条件の最適化:樹脂の種類や温度、圧力などを調整することで、冷却時間や充填時間を短縮できます。
注目される世界初の新材料
そこで今、注目されているのが 「MTA-FeX2」です。
熱伝導率90 W/m·Kを誇るFeX2は、例えばNAK80(約30 W/m·K)の約3倍の熱伝導性を持ち、エジソンハード窒化処理やカニボロンメッキ等で表面硬度がHRC60以上にあがり、冷却時間の劇的な短縮が可能です。
🔁 なぜハイサイクルが重要なのか?
⏱ 「1秒の短縮」が、利益に直結
たとえば、1個あたりの成形時間が1秒短縮されるだけで、 毎月500万個生産する場合、以下のような計算になります。
💰【コスト試算】1秒短縮でどれだけ削減できるか?
▸ 試算条件
- 生産数:月500万個
- 1秒短縮:500万秒の節約/月=約1,389時間
- 射出成形機チャージ単価:¥5,000/時間
- 人件費(作業者・保全含む):¥2,000/時間
▸ 削減コスト(月間)
項目 | 削減量 |
成形機稼働費 | 1,389時間 × ¥5,000 = ¥6,945,000 |
人件費 | 1,389時間 × ¥2,000 = ¥2,778,000 |
合計コスト削減 | 約¥9,723,000/月 |
▸ 年間では?
¥9,723,000 × 12ヶ月 = 約¥1億1,667万円の削減と試算されました。
結論:サイクル短縮は、即コスト削減に直結
あくまで例ではありますが、上記条件の場合、わずか1秒の違いでも、量産規模の現場では1億円規模の利益差を生みます。
つまり、ハイサイクル化は単なる「スピード」ではなく、事業の競争力そのものです。
FeX2搭載金型なら、この1秒以上の短縮が狙える
高熱伝導合金FeX2は、NAK80や一般的な金型鋼材に比べて、 冷却時間を3〜5秒短縮する事例もあります。
つまり、1個あたり3〜5秒の短縮 = 月間最大2〜3億円規模のコスト改善も現実的です。